Расчет размера по роликам зубчатого колеса. Размеры колеса схема
Устройство автомобиля в схемах - Колеса
Колеса
Автомобильное колесо: 1 - шина; 2 - обод; 3 - соединитель; 4 - ступица
Пневматическая шина сглаживает дорожные неровности и вместе с подвеской, смягчая и поглощая толчки и удары от неровности дороги, обеспечивает плавность хода автомобиля, а также надежное сцепление его колес с поверхностью дороги.
Ступица обеспечивает установку колеса на мосту на подшипниках и создает возможность колесу вращаться. При отсутствии ступицы вращающейся посадочной частью колеса является фланец полуоси, размещенной в балке моста на подшипниках.
На автомобилях применяют различные типы колес
Типы колес
Ведущие колеса преобразуют крутящий момент, подводимый от двигателя через трансмиссию, в тяговую силу, а свое вращение — в поступательное движение автомобиля.
Управляемые и поддерживающие колеса являются ведомыми; они воспринимают толкающую силу от рамы или кузова и преобразуют поступательное движение автомобиля в их качение.
Комбинированные колеса выполняют функции ведущих и управляемых одновременно.
Дисковые колеса из стального листа в качестве соединителя ступицы и обода колеса имеют стальной штампованный диск, приваренный к ободу. В литых колесах из легких сплавов (алюминиевых, магниевых) диск отливается совместно с ободом колеса. Дисковые колеса применяют на легковых и грузовых автомобилях малой и средней грузоподъемности.
Бездисковые колеса имеют соединитель, изготовленный совместно со ступицей; их выполняют в продольной и поперечной плоскостях.
Спицевые колеса в качестве соединителя обода и ступицы имеют проволочные спицы.
Типы, размеры и маркировка шин
На автомобилях применяют шины различных типов, предназначенные для эксплуатации при температуре окружающей среды от -45 до +55 °С.
Типы шин
Размеры и маркировка шины проставлены на ее боковой поверхности. Основными размерами шины являются ширина В и высота Н профиля, посадочный d и наружный D диаметры. Размер диагональных шин обозначается двумя числами — в виде сочетания размеров B—d. Для выпускаемых отечественных шин принята дюймовая система обозначения, т. е. размеры даются в дюймах (например, 6,95—16).
Основные размеры шин:В и Н— ширина и высота профиля; d и D — посадочный и наружный диаметры
Размер радиальных шин обозначается тремя числами и буквой R (например, 175/70/J13, где 175 — ширина профиля шины В, мм; 70 — отношение высоты Н к ширине профиля В, %; R — условное обозначение радиальной шины; 13 — посадочный диаметр d, дюймы). Кроме размеров в маркировке шины указывают завод-изготовитель, модель шины, ее порядковый номер и другие данные. На шины при необходимости наносят дополнительные обозначения.
Камерные и бескамерные шины
Камерная шина состоит из покрышки 10, камеры 9 и ободной ленты 2 (в шинах легковых автомобилей ободная лента отсутствует).
Камерная (а) и бескамерная (б) шины:1 и 12 — вентили; 2 —лента; 3— сердечник; 4— борт; 5— боковина; 6— каркас; 7 — подушечный слой; 8 — протектор; 9 — камера; 10 — покрышка; 11 — воздухонепроницаемый слой
Покрышка шины воспринимает давление сжатого воздуха, находящегося в камере, предохраняет камеру от повреждений и обеспечивает сцепление колеса с дорогой. Покрышки изготовляют из резины и специальной ткани — корда. Резина, используемая для производства покрышек состоит из каучука (натурального или синтетического), к которому добавляют серу, сажу, смолу, мел, переработанную старую резину и другие примеси и наполнители. Покрышка состоит из протектора 8, подушечного слоя (брекера) 7, каркаса 6, боковин 5 и бортов 4 с сердечниками 3. Каркас является основой покрышки. Он соединяет все ее части в одно целое и придает покрышке необходимую жесткость, обладая высокой эластичностью и прочностью. Каркас выполнен из нескольких слоев корда толщиной 1 ... 1,5 мм.
Корд представляет собой специальную ткань, состоящую в основном из продольных нитей диаметром 0,6...0,8 мм с очень редкими поперечными нитями. В зависимости от типа и назначения шины корд может быть хлопчатобумажным, вискозным, капроновым, перлоновым, нейлоновым и металлическим.
Протектор обеспечивает сцепление шины с дорогой и предохраняет каркас от повреждения. Его изготовляют из прочной, твердой, износостойкой резины. В нем различают расчлененную часть (рисунок) и подканавочный слой. Ширина протектора составляет 0,7...0,8 ширины профиля шины, а толщина — 10...20 мм у шин легковых и 15... 30 мм у шин грузовых автомобилей. Рисунок протектора зависит от типа и назначения шины.
Подушечный слой (брекер) связывает протектор с каркасом и предохраняет каркас от толчков и ударов, воспринимаемых протектором от неровностей дороги (у шин легковых автомобилей подушечный слой иногда отсутствует). Он обычно состоит из нескольких слоев корда (толщина подушечного слоя 3... 7 мм). Подушечный слой работает в наиболее напряженных темпе ратурных условиях по сравнению с другими элементами шины (до 110... 120°С).
Боковины предохраняют каркас от повреждений и действия влаги. Их обычно изготовляют из протекторной резины толщиной 1,5...3,5мм.
Борта надежно укрепляют покрышку на ободе. Снаружи борта имеют один-два слоя прорезиненной ленты, предохраняющей их от истирания об обод и от повреждений при монтаже и демонтаже шины. Внутрь бортов заделаны стальные проволочные сердечники, которые увеличивают прочность бортов, предохраняют их от растягивания и предотвращают соскакивание шины с обода колеса. Шина с поврежденным сердечником непригодна для эксплуатации.
Камера удерживает сжатый воздух внутри шины. Это эластичная резиновая оболочка в виде замкнутой трубы. Для плотной посадки (без складок) внутри шины размеры камеры несколько меньше, чем внутренняя полость покрышки. Толщина стенки камеры обычно составляет 1,5 ...2,5 мм для шин легковых автомобилей и 2,5... 5 мм для грузовых автомобилей и автобусов. На наружной поверхности камеры имеются радиальные риски, которые способствуют отводу наружу воздуха, остающегося между камерой и покрышкой после монтажа шины. Камеры изготовляют из высокопрочной резины.
Для накачивания и выпуска воздуха камера имеет специальный клапан — вентиль. Он позволяет нагнетать воздух внутрь камеры и автоматически закрывает его выход из камеры.
Ободная лента, устанавливаемая между ободом колеса и камерой шины, предохраняет камеру от повреждений и трения об обод колеса и борта покрышки. Лента исключает также возможность защемления камеры между бортами покрышки и ободом. Она выполнена из резиновой профилированной ленты и имеет форму кольца, внутренний диаметр которого несколько больше диаметра обода колеса.
Бескамерная шина по устройству близка к покрышке камерной шины и по внешнему виду почти не отличается от нее. Особенностью бескамерной шины является отсутствие камеры и наличие на ее внутренней поверхности герметизирующего воздухонепроницаемого резинового слоя 11 толщиной 1,5... 3 мм, который удерживает сжатый воздух внутри шины. На бортах шины, кроме того, имеется уплотняющий резиновый слой, обеспечивающий необходимую герметичность в местax соединения бортов и обода колеса. Материал каркаса шины также характеризуется высокой воздухонепроницаемостью, так как для него используют вискозный, капроновый или нейлоновый корд. Бескамерные шины по сравнению с камерными повышают безопасность движения, легко ремонтируются, во время работы меньше нагреваются, более долговечны, проще по конструкции, имеют меньшую массу.
Рисунок протектора шины
Рисунки протектора шин (а...д) и шипы противоскольжения (е):1 — сердечник; 2 — корпус
Большое влияние на движение автомобиля оказывает рисунок протектора шины.
Дорожный рисунок протектора (рис. а) имеют шины, предназначенные для работы на дорогах с твердым покрытием. Он обычно представляет собой продольные зигзагообразные ребра и канавки. Рисунок такого типа придает протектору высокую износостойкость, обеспечивает бесшумность работы шины и достаточную сопротивляемость заносу.
Кроме того, легковые шины могут иметь дорожный направленный рисунок протектора и дорожный асимметричный рисунок.
Шины с направленным рисунком протектора лучше отводят воду и грязь из места контакта их с дорогой, чем шины с обычным дорожным рисунком. Эти шины создают меньше шума. Однако рисунок запасного колеса при его установке совпадает по направлению вращения только с рисунком колес одной стороны автомобиля. Временная установка его против указанного направления вращения допустима только при условии движения с меньшей скоростью.
Шины с асимметричным рисунком протектора хорошо работают в различных условиях эксплуатации. Так, наружная сторона этих шин лучше работает на твердой дороге при положительной температуре, а внутренняя — в зимних условиях при пониженной температуре.
Универсальный рисунок протектора (рис. б) используют для шин автомобилей, эксплуатируемых на дорогах смешанного типа (с твердым покрытием и грунтовых). Протектор с таким рисунком имеет мелкую насечку в центральной части и более крупную — в боковой. При движении по плохим дорогам боковые выступы входят в зацепление с грунтом, в результате чего улучшается проходимость. Однако при таком рисунке повышается изнашивание протектора во время движения по сухим твердым дорогам. Рисунок обеспечивает хорошее сцепление на грунтовых дорогах, а также на мокрых, грязных и заснеженных дорогах с твердым покрытием.
Универсальный рисунок протектора также называется всесезонным, а шины с универсальным рисунком — всесезонными. Рисунок повышенной проходимости (рис. в) имеют шины, предназначенные для эксплуатации в тяжелых дорожных условиях и в условиях бездорожья. Он характеризуется высокими грунтозацепами. Протектор с таким рисунком обеспечивает хорошее сцепление с грунтом и хорошее самоочищение колес от грязи и снега между грунтозацепами. При движении по дорогам с твердым покрытием ускоряется изнашивание шин с этим рисунком протекгора, возрастает шум, ухудшаются плавность хода и устойчивость автомобиля.
Карьерный рисунок протектора (рис. г) имеют шины, предназначенные для работы в карьерах, на лесозаготовках и т. п. Этот рисунок аналогичен рисунку повышенной проходимости, но имеет более широкие выступы и более узкие канавки. Выступы выполняются массивными, широкими в основании и суживающимися кверху. Карьерный рисунок протектора обеспечивает высокое сопротивление шины механическим повреждениям и изнашиванию.
Зимний рисунок протектора (рис. д) предназначен для шин, эксплуатируемых на заснеженных и обледенелых дорогах. Он состоит из отдельных резиновых блоков угловатой формы, расчлененных надрезами, и достаточно широких и глубоких канавок. Площадь выступов зимнего рисунка составляет 60...70 % площади беговой дорожки протектора. Протектор с зимним рисунком обладает хорошей самоочищаемостью и интенсивным отводом влаги и грязи из зоны контакта. При движении по сухим дорогам с твердым покрытием, особенно в летнее время, шины с зимним рисунком протектора ускоренно изнашиваются, имеют значительное сопротивление качению и большую шумность. Эти шины допускают движение с максимальной скоростью на 15...35% ниже, чем обычные шины.
Зимний рисунок протектора обеспечивает возможность установки шипов противоскольжения для повышения безопасности движения на обледенелых и укатанных заснеженных дорогах. С этой целью в протекторе шины делают гнезда для шипов. Ошипованные шины повышают сцепление колес на скользких и обледенелых дорогах, на 40... 50 % сокращают тормозной путь, значительно повышают безопасность криволинейного движения и сопротивление заносу. Ошипованные шины следует применять на всех колесах автомобиля, частичная установка их приводит к нарушению безопасности движения. Давление в шинах с шипами на 0,02 МПа выше, чем в обычных шинах.
Шипы противоскольжения (рис. е) применяют на современных пневматических шинах. Шип состоит из корпуса 2 и сердечника 1. Сердечник делают из твердого сплава, обладающего высокой износостойкостью и вязкостью, корпус — обычно из сплава стали и свинца. Его оцинковывают, хромируют для защиты от коррозии. Иногда корпус шипа изготовляют пластмассовым. Диаметр шипа зависит от его назначения: для шин легковых автомобилей применяют шипы диаметром 8...9 мм.
Длина шипа в зависимости от толщины протектора шин составляет 10 мм и более.
Число шипов, устанавливаемых в шине, зависит от массы легкового автомобиля, мощности двигателя и условий эксплуатации.
В месте контакта шины с дорогой должно быть 8... 12 шипов. Наибольшая эффективность достигается, если длина выступающей части шипов составляет 1... 1,5 мм для шин легковых автомобилей.
Профиль шин
Широкопрофильные шины с двумя (а) и одной (б) беговыми дорожками
Применяемые на автомобилях шины могут иметь различную форму (профиль) поперечного сечения.
Шины обычного профиля (тороидные) выполняют камерными и бескамерными. Их профиль близок к окружности. Отношение высоты Я профиля шины к его ширине В составляет 0,9... 1,0. Эти шины распространены в наибольшей мере. Их устанавливают на легковых и грузовых автомобилях, автобусах, прицепах и полуприцепах, эксплуатируемых преимущественно на благоустроенных дорогах.
Широкопрофилъные шины (рис. а, б) имеют профиль овальной формы, отношение Н/В =0,6...0,9. Такие шины также могут быть камерными и бескамерными. Они работают как с постоянным, так и с переменным давлением воздуха. Выполняют их с одной или двумя выпуклыми беговыми дорожками. Нормальное внутреннее давление воздуха для широкопрофильных шин примерно в 1,5 раза ниже, чем для обычных.
Широкопрофильные шины с регулируемым давлением и одной беговой дорожкой применяют на автомобилях для повышения их проходимости, а с постоянным давлением и двумя беговыми дорожками — на автомобилях ограниченной проходимости для замены обычных шин сдвоенных задних колес. При этом достигаются снижение расхода материалов на 10...20% и уменьшение массы колес на 10... 15 %. По сравнению с обычными шинами 4 широкопрофильные имеют повышенную грузоподъемность и пониженное сопротивление качению. Они улучшают управляемость, устойчивость и повышают проходимость автомобиля, а также уменьшают расход топлива. Недостатком широкопрофильных шин является необходимость использования на одном автомобиле шин двух типов (обычных и широкопрофильных) и соответственно двух запасных колес (для переднего и заднего мостов) в тех случаях, когда они устанавливаются на сдвоенные задние колеса вместо обычных шин.
Низкопрофильные шины имеют Н/В =0,7...0,88, а сверхнизкопрофильные — не более 0,7. Те и другие шины повышают устойчивость и управляемость автомобиля. Они предназначены главным образом для легковых автомобилей и автобусов.
Специальные шины:а — арочные; б — пневмокаток; в — с регулируемым давлением
Арочные шины (рис. а) получили свое название от формы профиля — арки переменной кривизны с низкими мощными бортами {Н/В =0,35...0,5). Каркас шин прочный, тонкослойный, обладает малым сопротивлением изгибу. Арочные шины выполняют бескамерными. Внутреннее давление воздуха составляет 0,05... 0,15 МПа. Ширина профиля арочных шин в 2,5... 3,5 раза больше, чем у обычных, а радиальная деформация выше в 2 раза. Протектор арочной шины имеет рисунок повышенной проходимости с мощными расчлененными грунтозацепами эвольвентной формы почти на всю ширину профиля шины. Высота грунтозацепов составляет 35 ...40 мм, а шаг между ними — 100... 250 мм. В средней части рисунка протектора по окружности шины находится специальный пояс, состоящий из одного или двух рядов расчлененных грунтозацепов и предназначенный для уменьшения изнашивания протектора шины при движении по дороге с твердым покрытием. Широкий профиль с высокими грунтозацепами, эластичность шины и низкое давление воздуха обеспечивают большую площадь контакта протектора с опорной поверхностью, малое удельное давление, небольшое сопротивление качению и возможность реализации большой тяговой силы на мягких грунтах. При качении по мягкому грунту арочные шины интенсивно уплотняют его в направлении к центру контакта шин с опорной поверхностью. Вследствие этого значительно повышается проходимость автомобиля в условиях бездорожья (по размокшим грунтам, заснеженным дорогам и т. п.). Арочные шины используют как сезонное средство повышения проходимости автомобилей. Их устанавливают вместо обычных шин — сдвоенных задних колес на специальном ободе. По сравнению с обычными шинами арочные имеют более высокую стоимость, повышенный износ протектора на дорогах с твердым покрытием и более сложные монтаж и демонтаж.
Пневмокатки (рис. б) представляют собой высокоэластичные оболочки бочкообразной формы. Ширина П-образного профиля составляет 1 ...2 наружных диаметра пневмокатка, а отношение Н/В= 0,25...0,4. Протектор снабжен невысокими, редко расположенными грунтозацепами, которые наряду с основным своим назначением повышают прочность пневмокатка и обеспечивают сохранность (устойчивость) его формы. Эластичность пневмокатков в 3...4раза выше, чем у обычных шин, и в 1,5...2 раза выше, чем у арочных. Пневмокатки изготовляют бескамерными. Внутреннее давление воздуха в них 0,01 ...0,05 МПа. Высокая эластичность и малое внутреннее давление воздуха обеспечивают пневмокаткам очень низкое давление на грунт, хорошую приспособляемость к дорожным условиям и высокую сопротивляемость к проколам и повреждениям. В случае прокола воздух из пневмокатка выходит очень медленно из-за незначительного внутреннего давления. Однако по этой же причине пневмокатки при достаточно больших размерах имеют относительно малую грузоподъемность. Значительная ширина и малая грузоподъемность ограничивают применение пневмокатков на автомобилях. Кроме того, на ровных дорогах с твердым покрытием пневмокатки имеют относительно низкий срок службы.
Пневмокатки предназначены для автомобилей, работающих в особо тяжелых условиях. Их монтируют на ободьях специальной конструкции. Автомобили с пневмокатками могут двигаться по снежной целине, сыпучим пескам, заболоченной местности и т, п.
Диагональные и радиальные шины
Диагональная (а) и радиальная (б) шины:1 — подушечный слой; 2 — каркас
Конструкции каркаса диагональной и радиальной шин различны. В каркасе 2 (рис. а) диагональной шины нити корда расположены под углом 50...52й к оси колеса и перекрещиваются в смежных слоях. Нити корда подушечного слоя 1 также расположены под некоторым углом к оси колеса. Каркас диагональной шины менее подвержен повреждению от ударов, порезов и т. п.
Радиальная шина (рис. б) отличается от диагональной расположением нитей корда в каркасе, формой профиля, слойностью, особенностями подушечного слоя, бортовой части и протектора, качеством применяемых материалов.
Нити корда шины расположены радиально, идут параллельно друг другу от одного борта шины к другому. Число слоев корда вдвое меньше, чем у диагональной шины. Подушечный слой 7 изготовлен из металлического или вискозного корда. Высота профиля шин несколько снижена — Н/В =0,7...0,85. Шины бывают камерными и бескамерными. Радиальные шины по сравнению с диагональными характеризуются большей грузоподъемностью (на 15...20%), большей радиальной эластичностью (на 30...35 %), меньшим сопротивлением качению (на 10 %), меньшим нагревом (на 20...30°С). Они лучше сглаживают микронеровности дороги, улучшают управляемость автомобиля, уменьшают расход топлива и обладают большей износостойкостью. Срок службы шин в 1,5... 2 раза выше, их пробег составляет 75...80 тыс. км. Однако шины имеют высокую стоимость и повышенную боковую эластичность.
Шины с регулируемым давлением
Шины с регулируемым давлением (см. рис. в) могут быть камерными и бескамерными. По сравнению с обычными шинами они имеют увеличенную ширину профиля (на 25...40%), меньшее число слоев корда каркаса (в 1,5...2раза), мягкие резиновые прослойки между его слоями, увеличенную площадь опоры на грунт (в 2...4 раза при снижении давления), меньшее удельное давление на грунт, хорошее сцепление с ним и большую эластичность. Протектор шин также отличается повышенной эластичностью и имеет специальный рисунок с крупными, широко расставленными грунтозацепами, допускающими большие деформации. Высота грунтозацепов 15... 30 мм. Вентиль шин не имеет золотника. Такие шины могут работать с переменным давлением воздуха 0,05...0,35 МПа, значение которого выбирает водитель в соответствии с дорожными условиями. Давление воздуха в шинах регулируют с помощью специального оборудования, которое позволяет не только поддерживать в шинах требуемое давление в зависимости от условий эксплуатации, но и непрерывно подавать воздух в шины при проколах и мелких повреждениях. Шины с регулируемым давлением применяют на автомобилях высокой проходимости для работы на дорогах всех категорий в любых климатических зонах страны при температурах от -60 до +55 °С. При прохождении тяжелых участков пути — заболоченной местности, снежной целины, сыпучих песков — давление воздуха в шинах снижают до минимума, а на дорогах с твердым покрытием доводят до максимального значения. В связи с тем что они работают в более тяжелых условиях и при пониженных давлениях воздуха, срок их службы в 2...2,5 раза меньше, чем у обычных шин. Кроме того, эти шины имеют пониженную грузоподъемность по сравнению с обычными шинами того же размера.
Обод, ступица и соединитель колеса
У колес автомобиля могут быть глубокие неразборные или разборные ободья, служащие для установки пневматической шины. Они имеют специальный профиль, их обычно штампуют или прокатывают из стали, а также отливают совместно с диском из легких сплавов (алюминиевых, магниевых).
Дисковые (а, б) и спицевое (в) колеса легковых автомобилей:1— диск; 2 — обод; 3 — спица; А и Б — отверстия; В — выемка
Глубокий обод 2 (рис. а) выполнен неразборным. В средней части обода сделана выемка В (симметричная или несимметричная), которая облегчает монтаж и демонтаж шины. По обе стороны выемки расположены конические полки, которые заканчиваются бортами. Угол наклона полок обода составляет 5+1 вследствие чего улучшается посадка шины на ободе.
Глубокие ободья отличаются большой жесткостью, малой массой и простотой изготовления. Однако на них можно монтировать шины сравнительно небольших размеров с высокой эластичностью бортовой части. Поэтому глубокие ободья используют только в колесах легковых автомобилей и грузовых автомобилей малой грузоподъемности.
Разборные ободья применяют для колес большинства грузовых автомобилей. Их конструкции весьма разнообразны. Разборный обод с конической посадочной полкой наиболее часто используют для камерных шин грузовых автомобилей. Обод 3 имеет неразрезное съемное бортовое кольцо 1 с конической полкой, которое удерживается на ободе с помощью пружинного разрезного кольца 2. Разборные ободья облегчают монтаж и демонтаж шин, имеющих большие массу, размеры и жесткую бортовую часть. Для шин с регулируемым давлением воздуха, широкопрофильных, арочных, а также некоторых шин грузовых автомобилей большой грузоподъемности применяют разборные ободья с разборными кольцами. Такой обод состоит из двух частей, соединяемых между собой болтами. Разборные ободья обеспечивают надежное крепление шины независимо от внутреннего давления воздуха в ней.
Ступица обеспечивает установку колеса на мосту и дает возможность колесу вращаться. Ступицы делают обычно из стали или ковкого чугуна, монтируют на мосту с помощью конических роликовых подшипников. Кроме колес к ступицам также крепят тормозные барабаны и фланцы полуосей (ведущие мосты грузовых автомобилей).
Ступица переднего колеса автомобиля ВАЗ повышенной проходимости (См. Передняя подвеска автомобиля ВАЗ повышенной проходимости)
Ступица переднего колеса переднеприводного автомобиля ВАЗ (см.Передняя подвеска переднеприводного автомобиля ВАЗ).
Ступица 1 заднего колеса (см. Задняя плдвеска переднеприводного автомобиля ВАЗ).
Соединитель колеса чаще всего выполняется в виде диска. Такие колеса называются дисковыми.
Бездисковые колеса имеют соединительную часть, изготовленную совместно со ступицей. Колеса делают разъемными в продольной или поперечной плоскости.
Конструкция (а) и крепление (б) бездискового колеса:1 — секторы; 2 — ступица; 3 — прижим; 4 — шпилька; 5— гайка
autocxema.ucoz.ru
Устройство колеса автомобиля. Типы конструкций и маркировка
Из различных книг и других источников информации можно узнать, что первые колеса появились примерно за три тысячи лет до нашей эры. Об этом свидетельствуют различные изображения, на которых были нарисованы первые в мире повозки и колесницы.
Одна из версий свидетельствует о том, что первые колеса создавали по образу солнца. Колесный круг считался божественным символом для некоторых племен и народов. Толщина обода колеса достигала больших размеров, из-за этого его масса была слишком большой. Соответственно, скорость транспорта была довольно низкая. Колесо имело вид деревянного диска, который насаживался на ось и закреплялся клином. Предшественником колеса был деревянный каток.
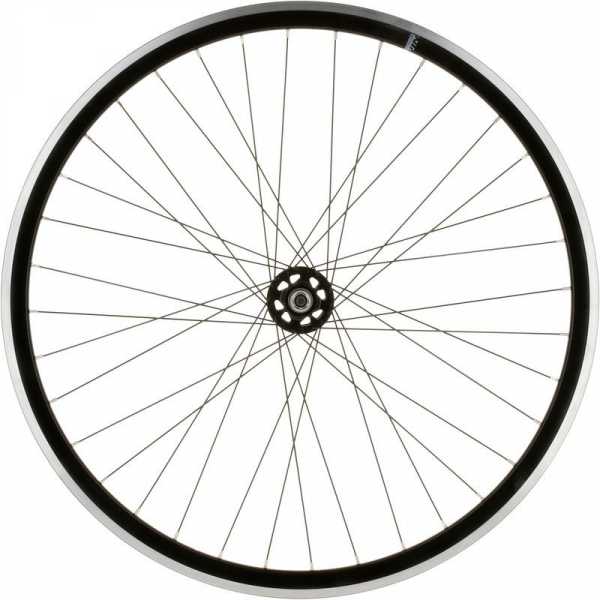
Колесо
Колеса первых автомобилей были деревянными и ничем не отличались от колес конных повозок. Затем люди придумали и создали колеса с деревянными спицами и металлическим ободом. Вскоре на смену деревянным спицам придумали спицы из проволоки, как у велосипедов и мотоциклов. Шины изготавливали в виде плоских резиновых лент. Через некоторый промежуток времени, благодаря техническому прогрессу, люди создали пневматические колеса.
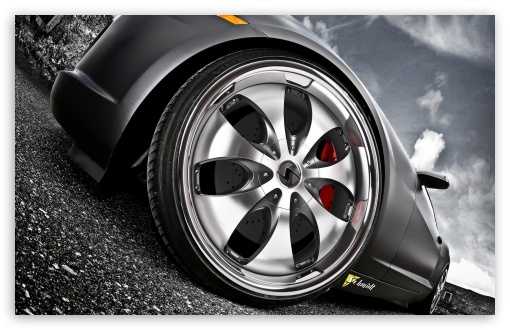
Особенность устройства колеса автомобиля заключается в том, что оно передает крутящий момент благодаря системе рычагов, и таким образом приводит в движение любое транспортное средство для передвижения. В современном мире колесо состоит из двух основных элементов, таких как резиновая шина и металлический диск. В наше время устройство колеса автомобиля упростили и сделали его намного прочнее и качественнее. Колеса бывают камерные и бескамерные. В бескамерных отсутствует камера между диском и покрышкой. Шина герметично прилегает к диску, сидя плотно на ободе. Колесо – важная часть автомобиля, оно состоит из обода и фланца.
Обод – это одна из частей колеса, на него надевается шина. Фланец - диск, расположенный в центральной части обода, с его помощью закрепляется колесо на ступице оси автомобиля. Обод является важной частью колеса.
Автомобильные колеса теперь доступны на всех мировых рынках. От качества колеса зависит его цена. Существуют сотни фирм, выпускающих шины для колес автомобилей. Давайте узнаем, зачем же нужна шина.
Она предназначена для надежного сцепления колеса и дорожного покрытия при движении и поворотах, а также для смягчения ударов; обеспечивает проходимость автомобиля на различных дорогах или по бездорожью. Шины делаются из натурального или синтетического каучука. Шина без камеры является покрышкой, которая состоит из корда, боковин и протектора. Самые огромные в мире шины для автомобилей выпускает компания Bridgestone. Они имеют маркировку 59/80R63, ширина 59 дюймов, внутренний радиус 63 дюйма, внешний - 80 дюймов. Эти шины устанавливаются на большие колеса. Их высота достигает четырех метров. Такой тип колес автомобиля имеет тяжелую конструкцию. На шине имеется протектор. Протектор - основой слой резины, отвечающий за сцепление колеса с дорогой, а также защищает внутренние части резины и всего колеса от повреждений при взаимодействии с дорожной поверхностью. Различают универсальный, дорожный или специальный. Шины изготавливают под все размеры диска колеса.
Шины классифицируются следующим образом:
- Камерные и бескамерные - по строению внутренней поверхности колеса.
- Диагональные - по строению каркаса. Диагональные шины - те, в которых установлено перекрестное расположение слоев корта. Угол их наклона составляет 35-38 градусов.
- Радикальные - по таких шинах расположение нитей корта параллельное, под прямым углом.
- Универсальные, сезонные (зимние и летние), повышенной проходимости – по ширине и высоте рисунка протектора на шинах.
Диски
Диск - это одна из частей устройства колеса автомобиля. Диски производят из различный металлов. Они состоят из следующих элементов, которые мы разберем подробней. Для тюнинга автомобиля выпускают специальные размеры дисков колеса. Диски измеряются в дюймах, к примеру: на 14 дюймов, на 17, на 21 и так далее.
- Боковины.
- Корд.
- Металлический каркас.
Борт предназначен для закрепления шины на ободе, а также для ее герметизации между диском. В основе борта - кольцо, сделанное из прорезиненной стальной проволоки. Борт является слоем корда, завернутого по кругу кольца из проволочного наполнительного резинового шнура. Обладая высокой прочностью и жесткостью за счет стального кольца и монолитности, а также наполнительного шнура, борт считается самой жесткой частью на диске. Он способен выдержать сильные удары.
Боковины состоят из тонкого слоя эластичной резины, который расположен между плечевой зоной и бортом. Боковина предназначена для защиты протектора шины от механических повреждений и попадания влаги, также она является продолжением протектора.
Корд – это то, что находится внутри резины. Он может быть сделан из металлических, стеклянных, полимерных нитей.
Диски делают из стали, алюминия, магния. Сталь используется для дешевых колес. Из алюминия делаются легкосплавные диски. Этот вид металла - легкий и недорогой, устойчив к коррозии. Марка используемого алюминия - 6061. Характеристика его свойств идеально подходит для изготовления колес.
Из магния производят колеса для гоночных авто. Диски получаются прочными и легкими. Изготовление такого типа колес требует наличия профессионального оборудования, так как процесс обработки магния очень сложен из-за его реакции на высокую температуру плавления. Также диски производят из карбона и титана. Из этих материалов получаются легкие и прочные колеса.
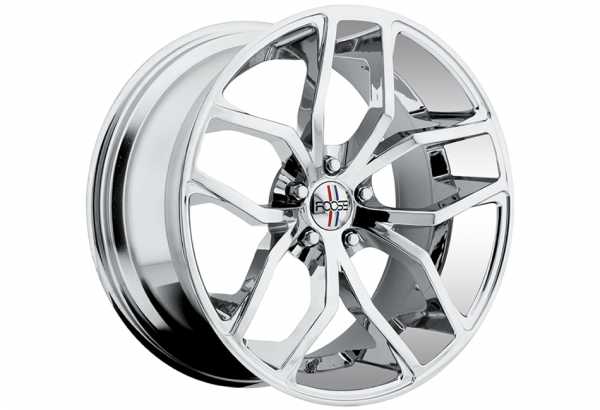
Маркировка колес
Наличие на шине надписи P195/55 R15 84 H означает ее размер и категорию. Приведем расшифровку:
- Р – обозначает категорию для легковых автомобилей, а 195 – это ширина шины в мм.
- 55 - это серия шины.
- R - конструкция шины (радикальная). Кстати, радиус никакого отношения к этой букве не имеет.
- 15 - диаметр диска.
- 84 - максимальная нагрузка на колесо (следует смотреть в специальных таблицах).
- H - максимальная скорость (также нужно смотреть в таблицах).
Еще указывается производитель шины, к примеру: Hada, Avon, Nitto, страна-изготовитель и знак предприятия, на котором сделан данный товар. Также имеются четыре цифры, которые обозначают дату изготовления.
Теперь разберем основные символы на шинах:
- MAX LOAD - допустимая максимальная нагрузка в кг.
- TUBE TYRE – шина с камерой.
- TUBELESS – шина бескамерная.
- MAX PRESSURE – допускаемый объем давления в шинах в кПа.
- REINFORCED – суперусиленная шина. Обладает уникальными свойствами.
- RADIAL – ширина радиальной конструкции.
- REGROOVABLE – максимальное углубление рисунка протектора при нарезке.
- DSI, TWI – расположение индикаторов износа.
- ALL STEEL - надпись предназначена для шин с каркасом и металлокордным брекером.
- M&S – всесезонные шины. Mud & Show – переводится как грязь+ снег.
- Rotation – обозначает, что шина имеет направление и на ней указана стрелка.
- All Season – шины, которые используют круглый год.
- Inside и Outside, а также Side Facing Inwards и Side Facing Out, - асимметричные шины. При установке бывают левые или правые, то есть Left или Right.
- AQUA, WATER, RAIN - обозначает, что шины обладают высокой защитой и устойчивостью при дождливой погоде.
- E – Европейский стандарт безопасности.
- DOT – стандарт безопасности США
- Traction А, В, С - способность к торможению на мокрой поверхности.
- Treadwear – износостойкость шины (пробег).
- Temperature А, В, С – термостойкость при высоких скоростях.
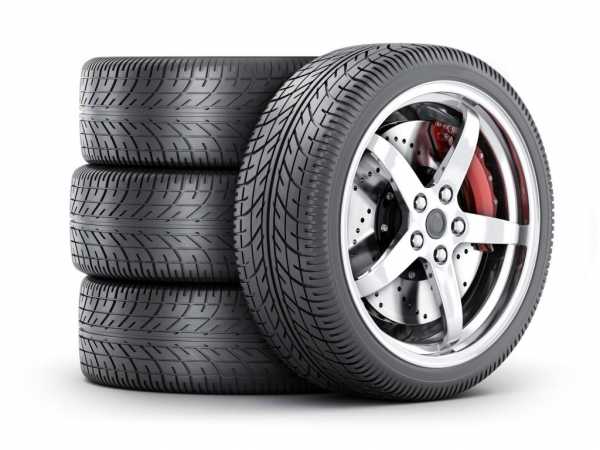
Примечание
Маркировка колес автомобилей зависит от категории автотранспорта, страны, климатических условий. Необходимо внимательно выбирать размер колеса. На грузовые автомобили на задние мосты и прицепы устанавливают по несколько пар. Большие колеса, малые, средние – на каждый вид покупается свой размер шины.
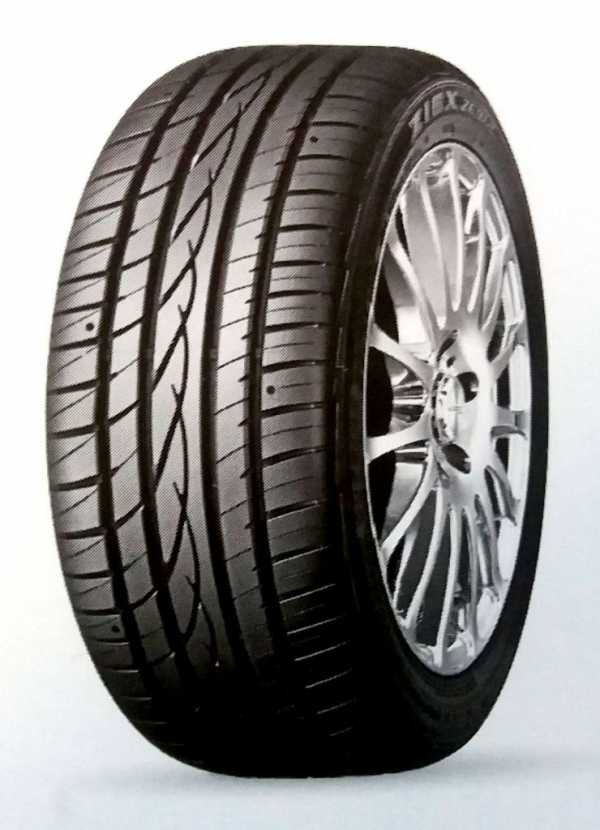
Ремонт колеса автомобиля
Нередко нам приходится сталкиваться с проблемами на дорогах. Одна из них – это повреждение дисков колес и прокол шин. Давайте рассмотрим, как можно справиться с этой проблемой.
Ремонт дисков колес зависит от его типа и материала изготовления. Как именно будет проводиться ремонт колес? С использованием каких технологий и сколько времени это займет? Во многом это зависит от самого диска. При ремонте дисков устанавливают небольшие грузики для дисбаланса. Ремонт колес автомобилей достаточно прост.
Диски бывают литые, кованые и штампованные. Литые диски – это самый распространенный вид. Для их изготовления применяют легкие сплавы металлов. В результате получается прочная и легкая конструкция, заметно легче стальных дисков и сделанная гораздо точнее. Литые диски легче, чем другие виды, но допустимый дисбаланс меньше, чем у штампованных. Штампованные диски намного слабее литых, они изготавливаются из прокатной углеродистой стали путем штампования. Кованые - еще менее распространенный вид дисков. Но они обладают преимуществом перед штампованными и литыми, намного прочнее и более износостойкие.
При повреждении литого диска используют не прокат, а правку, то есть вытягивают его на специальных станках. Сваркой наращивают утраченные при повреждении элементы. Штампованный диск восстанавливают прокатом. Это позволяет структура материала, из которого он сделан. Диск намного эластичней и поддается прокату. Кованые диски ремонтируются так же, как и литые.
Автомобильные колеса получают различные повреждения, которые часто можно самостоятельно устранить. Но при серьезных повреждениях лучше обратитесь в автосервис, воспользуйтесь эвакуатором. Автомобильные колеса, имеющие порезы и шинные шишки, являются опасными для езды. При обнаружении таких дефектов лучше сразу все исправить.
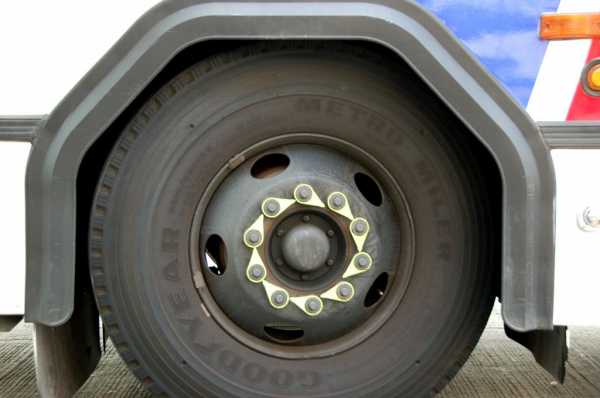
Ремонт шин
Давайте разберем, что собой представляет прокол. Это повреждение шинной части в области протектора. Имея инструмент и набор специальных заплаток, его можно устранить в любых условиях своими руками, а затем добраться до сервиса.
Боковой порез можно отремонтировать только на вулканизации. Это наиболее опасный тип повреждения колеса. Рекомендуется при себе иметь запасное колесо.
Заклеиваем прокол своими руками
Проделываем следующие действия:
- Снимаем и сдуваем колесо
- Вытаскиваем его из диска.
- Осматриваем место повреждения.
- Смотрим, чтобы жгут или заплатка, которую мы поставим, соответствовали размеру прокола.
- Очищаем поверхность от грязи и пыли.
- Затыкаем жгутом дырку, порез или прокол (можно использовать два жгута).
- Накачиваем колесо.
Рассмотрим следующий тип колеса
У грузовых автомобилей установлены бездисковые или дисковые колеса. У КАМАЗа колеса оснащены пневматическими шинами. Колеса подразделяются на ведомые и ведущие, а также комбинированные. Колесо грузовика состоит из обода и диска. Устройство колеса автомобиля грузового типа - особое. Диск оснащен плоским ободом. На грузовых автомобилях на заднюю ось устанавливают по два колеса. Диск внутреннего колеса крепится на шпильки колпачковыми гайками, а наружный прикручивается коническими. У гаек, расположенных с правой стороны, нарезана правая резьба, с левой стороны нарезана левая. Запасное колесо на КАМАЗ устанавливается сзади кабины. Оно подается специальным гидравлическим отводом. Также на некоторые типы грузовиков устанавливают неразборные колеса.

Бездисковые колеса применяются на грузовых автомобилях КАМАЗ и МАЗ. В настоящее время их используют для автобусов и тяжелогрузных автомобилей. Они состоят из спицевой ступицы и обода. Такие типы колес легко обслуживаются и восстанавливаются при повреждениях. На КАМАЗ колеса подбирают и устанавливают по специальной категории грузоподъемности.
Ступица колеса
Ступица - важная часть крепления колеса на ось. Оно крепится через подшипник. Подшипник колес является важной частью, так как от него зависит безопасность управления автомобилем. Также на ступицу устанавливают тормозной барабан или диск. Она обеспечивает вращательные движения колеса.
Подшипник крепится на ось упорной шайбой и гайкой. Зажимая или ослабляя гайку, мы прижимаем или расслабляем ролики. Таким образом производится регулировка для удаления люфта. Подшипник колеса не защищен от попадания грязи и пыли, поэтому требует постоянного ухода и облуживания. Сальник подшипника приходит в негодное состояние, из-за этого из него начинает вытекать смазочный материал. Обычно это происходит при нагревании детали или взаимодействии с водой. А при износе сальника в подшипник попадает грязь, пыль, песок. Это приводит к его износу и требует замены.
Подшипник с переднего колеса состоит из трех частей: обоймы (внешней и внутренней), кассеты с роликами. При установке их смазывают «Литолом». Это смазка, наносится она внутрь подшипника. Не рекомендуется вскрывать подшипник, а также заменять в нем смазку.
При износе подшипника его заменяют при помощи выпрессовки. Не рекомендуется выбивать его молотком. Прессовка позволяет легко извлечь изношенный подшипник из посадочного места.
Гайки
Основным элементом крепления колеса на ступицу являются гайки. Они имеют форму шестиугольника и бывают различных видов по форме резьбы и размеру. Их изготавливают из алюминия, хрома-ванадия, стали и титана.
Алюминиевые гайки очень дорогие. Их изготавливают для гоночных автомобилей. Они мало весят, это обеспечивает снижение лишнего веса колеса. Алюминиевые гайки мягкие и требуют постоянной затяжки колеса. При покупке обязательно уточните, какие точно подходят гайки на ваш автомобиль.
Гайки из хром-ванадия стоят столько же, как и алюминиевые. Но они намного тяжелее. Самые дорогие гайки - из титана, они применяются для тюнингованных автомобилей. Они очень прочные и легкие и превосходят по качеству все остальные изделия.
Стальные - это самые простые и популярные гайки. Являются самым распространенным видом на мировом рынке. Их различают по типу обработки: оцинкованные или хромированные. Они доступны по цене.
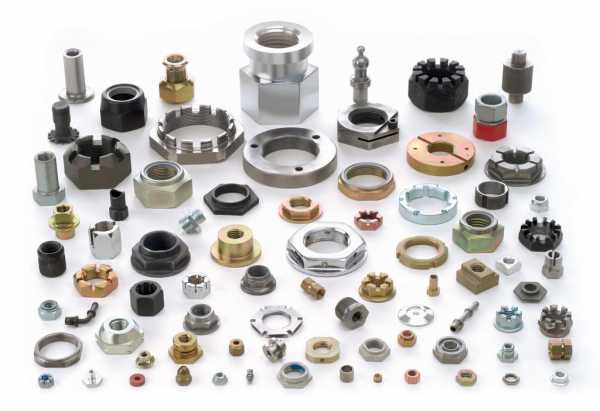
В заключение
Покупайте только качественные колеса, от них зависит безопасность управления автомобилем. При износе одного колеса рекомендуется менять пару.
fb.ru
Устройство автомобильного колеса — Энциклопедия журнала "За рулем"
Устройство автомобильного колеса:1 — шина;2 — обод;3 — ступица
Колесо автомобиля состоит из пневматической шины, обода, соединительного элемента (диска), ступицы и пневматических шин.В зависимости от конструкции обода и соединительного элемента колеса могут быть разборными и неразборными, дисковыми и бездисковыми. Ступица колеса обеспечивает его свободную установку на оси автомобиля.
Неразборное колесо с глубоким ободом
Обод служит для соединения шины с колесом. С этой целью ему придается специальная форма. Колесо в сборе должно быть сбалансировано, балансировочные грузики крепятся к ободу с помощью пружинных зажимов или клея. На большинстве легковых автомобилей и грузовых небольшой грузоподъемности используются глубокие, неразборные ободья.Глубокий обод жестко соединяется с диском, который служит для крепления колеса к ступице с помощью болтов или гаек со шпильками. Полки глубокого обода имеют конусную форму для плотной посадки шины на обод. Угол наклона полок составляет, как правило (5±1)°. Полки обода заканчиваются закраинами, имеющими определенную форму и служащих боковыми упорами для шины.Расстояние между закраинами называется шириной профиля обода. В средней части обода имеется углубление, необходимое для облегчения монтажа и демонтажа шины на обод. Это углубление (ручей) может быть расположено симметрично относительно плоскости колеса или со смещением.
Размеры и профиль обода регламентированы соответствующими стандартами. На каждый обод наносится соответствующая маркировка, из которой можно узнать размеры и профиль. Основные размеры обода, ширину профиля и диаметр, как правило, все изготовители указывают в дюймах, за исключением компании Michelin, которая применяет для этого миллиметры.Пример маркировки: 5J × 13h3 ET 30, где:5 — ширина обода в дюймах;13 — диаметр обода в дюймах;J и h3 — конструктивные особенности профиля обода;ET 30 — вылет (от немецкого слова Einpresstiefe — ET) 30 мм.
Положительное (а) и отрицательное (б) плечо обката управляемого колеса
Вылет колеса (выступ) является важным параметром. Любое колесо должно «охватывать» ступицу, к которой оно крепится, потому что центр пятна контакта шины с дорогой смещается относительно вертикальной оси, проходящей через центр ступицы на небольшую величину, которая рассчитывается при конструировании подвески и рулевого управления автомобиля.Величина вылета особенно важна для управляемых колес, потому что положение пятна контакта относительно оси поворота колеса играет важную роль в определении характеристик поворота автомобиля.
Неразборные колеса с глубоким ободом обычно центрируются на ступице с помощью центрального отверстия. Если диаметр центрального отверстия больше, чем у посадочной части ступицы, то центрирование осуществляется по коническим (или сферическим) поверхностям в отверстиях диска, предназначенных для крепления болтами или гайками. Иногда для лучшего центрирования и облегчения монтажа используют пластмассовые кольца, которые устанавливаются перед монтажом колеса на ступицу в центральное отверстие диска.Колесные диски легковых автомобилей изготавливаются штамповкой из стали с последующей сваркой обода и диска или из легких сплавов (алюминиевых или магниевых). Наиболее прочные колеса из легких сплавов — кованые. Они имеют мелкозернистую структуру и высокую прочность при малой массе. Легкосплавные колеса дороже стальных, но эстетически привлекательнее. Колеса изготавливались и из композитных материалов: например, еще в 70-е гг. фирма Citroёn выпускала армированные углепластиковые колеса, которые весили в два раза меньше металлических. Однако из-за высокой стоимости таких колес они устанавливаются только на дорогих спортивных автомобилях.
Конструкция разборного обода грузового автомобиля:1 — закраина;2 — обод;3 — разрезная часть обода;М — ширина обода;D — диаметр обода
Разборные ободья применяют для колес большинства грузовых автомобилей и автобусов. Разборные ободья могут быть дисковыми и бездисковыми. Наиболее часто используются разборные ободья с коническими посадочными полками.
Бездисковое колесо, его общий вид (а) и крепление колеса (б):1 — секторы колеса;2 — ступица;3 — крепление;4 — шпилька;5 — гайка
Шины грузовых автомобилей имеют большие размеры и высокую жесткость, поэтому монтаж таких шин на неразборные ободья затруднен. Разборные ободья позволяют облегчить эту задачу. Для некоторых шин грузовых автомобилей большой грузоподъемности применяют разборные ободья с распорными кольцами. Такие ободья состоят из двух частей, соединяемых между собой болтами. Такая конструкция надежно удерживает шину на колесе независимо от значения давления воздуха в шине.Ступицы колес изготавливают из стали или ковкого чугуна. К ним крепятся элементы тормозных механизмов, диски и барабаны. Ступица устанавливается на подшипниках, которые должны воспринимать не только радиальные, но и осевые усилия от действия боковых сил. В ступицах устанавливают конические роликовые или шариковые радиально-упорные подшипники.В подшипники колес закладывается смазка, выдерживающая высокие температуры. Для предотвращения вытекания смазки и попадания грязи подшипники уплотняются сальниками.
Подробнее о колесном диске - в главе Колесный диск
wiki.zr.ru
Колеса Камаз
Устройство колес. Автомобили КамАЗ с клееной формулой 6X4 включают два одинарных передних управляемых колеса четыре сдвоенных задних ведущих колeca.
Передние колеса автомобилей КамA3 — бездисковые со спицевыми ступицами, с разъемными ободами и пневматическими шинами, имеющими универсальный рисунок протектора.
Установка переднего колеса:1 — правый поворотный кулак, 2 — гайка подшипников, 3 — замковая шайба гайки подшипников, 4 — замковая шайба контргайки, 5 — контргайка, 6 — крышка ступицы переднего колеса, 7, 14 — подшипник; 8 — гайка самоконтрящаяся, 9 — ступица, 10 — гайка. 11 — прижим, 12 — замочное кольцо, 13 — бортовое кольцо, 15 — упорное кольцо, 16 — кольцо манжеты, 17 — маслоуловитель переднего тормоза, 18 — тормозной барабан, 19 — колодка тормоза с накладкой, 20 — обод колеса, 21 — манжета, 22 — щиток тормоз 23 — суппорт, 24 — упор поворотного кулака, 25 — продольная тяга, 26 — рычаг тяги сошки, 27 — вал передней оси, 28 — рычаг поворотного кулака, 29 — поперечная тяга, 30—камера, 31 — покрышка, 32 — ободная лента
Переднее колесо (рис.) состоит из ступицы 9, обода 20 и шины. В центре ступицы имеется полость, в которой расположены гнезда для установки подшипников 7 и 14 и манжеты 21 ступицы. На ступице пять спиц, равномерно расположенных по окружности. Концы спиц заканчиваются коническими опорами, предназначенными для посадки конической поверхности обода. Угол конуса 28 ° обеспечивает при затяжке гаек 10 силу трения, необходимую для надежного соединения обода со ступицей и предохранения его от проворачивания при торможении. Шпильки крепления ободов к ступицам колес имеют правую резьбу. В теле ступицы между спицами имеется пять отверстий, предназначенных для болтов крепления тормозного барабана 18. Гайки 10 болтов самоконтрящиеся. Для уменьшения изнашивания шин и улучшения устойчивости и управляемости автомобиля ступица в сборе с тормозным барабаном балансируется. Допустимый дисбаланс 700 Нм. Для устранения дисбаланса на производстве сначала определяют наиболее тяжелое место ступицы с барабаном в сборе, а затем с противоположной стороны к наружной поверхности тормозного барабана приваривают груз. Масса груза определяется величиной устраняемого дисбаланса. Обод колеса с конической посадочной полкой разборный. Он состоит непосредственно из обода 20, замочного кольца 12 и бортового кольца 13. Полка обода с одной стороны заканчивается бортом, с другой стороны — фасонным сечением, предназначенным для посадки на конические поверхности спиц и размещения бортового и замочного колец. Замочное кольцо разрезное. Оно изготовлено из специального стального профиля. Бортовое кольцо также стальное.
Шина пневматическая, камерная с радиальным кордом и универсальным рисунком протектора. Маркировка шины 260-508Р, что означает: 260 — ширина профиля надутой шины в мм, 508— наружный диаметр обода, Р — шина с радиальным кордом.
Шина с ободом в сборе балансируется относительно конической поверхности и торца обода. Допустимый дисбаланс 0,3 Нм. Дисбаланс устраняется установкой балансировочных грузов. Количество грузов в зависимости от устраняемого дисбаланса может быть разное, но не должно превышать пяти. При установке груза должны быть исключены удары по нему и пружине. Груз должен быть плотно прижат к замочному кольцу, выступание одного груза относительно соседних не должно превышать 3 мм.
Рис. 2 Установка заднего колеса:1— шпилька крепления полуоси, 2 — разжимная втулка, 3 — пружинная шайба, 4,5 — гайки, 6 — шайба отгибная, 7 — шайба замочная, 8 — гайка, 9 — прижим, 10, 12 — подшипники, 11 — ступица, 13 — проставочное кольцо, 14 — замочное кольцо, 15 — кольцо манжеты, 16 — бортовое кольцо, 17 — маслоуловитель, 18 — тормозной барабан, 19 — суппорт, 20 — щиток тормоза, 21 — колодка тормоза с накладками, 22 —шина
Задние колеса автомобилей КамАЗ 6X4 также бездисковые. Обод (рис.) внутреннего колеса установлен на конической поверхности спиц задней ступицы 11. Расстояние между шинами сдвоенных колес обеспечено проставочным распорным кольцом 13, которое для увеличения жесткости выполнено гофрированным. Это кольцо передает также на внутреннее колесо усилие затяжки гаек 8 и прижимов 9, крепящих наружное колесо. Прижимы задних колес отличаются от прижимов передних колес, так как имеют скос, который одновременно центрирует и зажимает обод наружного колеса.
Ступицы вращаются на конических подшипниках 10 и 12, установленных на цапфах ведущих мостов, закреплены одной гайкой 5 с двумя шайбами: замочной 7 и отгибной 6.
Запасные колеса автомобилей с колесной формулой 6X4 (кроме автомобиля-самосвала КамАЗ-5511) установлены в горизонтальном положении над правым лонжероном на кронштейне 10 (рис. ), который закреплен пятью болтами на лонжероне рамы. На этом же кронштейне установлен механизм подъема и опускания запасного колеса. Вал 4 ворота от проворачивания в обратном направлении удерживается храповиком 3 и защелкой 8, которая постоянно прижата к храповику пружиной 7.
Установка запасного колеса автомобиля КамАЗ-5320:1 — гайка, 2 — тарельчатая пружина, 3 — храповик ворота, 4 —вал ворота, 5 — трос, 6 — гайка, 7 — пружина защелки, 8 —защелка ворота, 9 — опора, 10 — кронштейн
Для подъема колеса вал вращают за квадратный хвостовик баллонным ключом, трос 5 наматывается на вал и поднимает опору 9 вместе с колесом. В поднятом положении колесо фиксируют гайкой 6.
На автомобилях-самосвалах КамАЗ-5511 запасное колесо закреплено на переднем борту платформы. Подъем и опускание колеса осуществляют с помощью механизма 1 (рис. 4) тросом 2, который пропущен через блок 3.
Рис. 4 Установка запасного колеса автомобиля-самосвала КамАЗ-5511
Рис. 5 Колесо автомобиля КамАЗ-4310: 1 — замочное кольцо, 2,4 — бортовые кольца, 3 —шина с камерой и ободной лентой, 5 — обод
На автомобилях повышенной проходимости с колесной формулой 6X6 все колеса одинарные, что уменьшает сопротивление движению автомобиля. Колеса дисковые, с тороидальной поверхностью посадочных полок обода 5 (рис.). Они снабжены двумя бортовыми кольцами 2 и 4, замочным кольцом 1 и широкопрофильной шиной 3 с рисунком протектора повышенной проходимости. Модель применяемой шины — ИП184, размер 1220 X 400—533, что означает: 1220 мм — наружный диаметр шины, 400 мм — ширина профиля, 533 — наружный диаметр обода. Конические поверхности обода и бортовых колец обеспечивают посадку шины с натягом, что позволяет работать при пониженном давлении воздуха в ней. Колеса к ступицам крепятся десятью шпильками и гайками. Ступицы колес на цапфах мостов автомобилей с колесной формулой 6X6 закреплены так же, как и ступицы передних колес автомобилей с колесной формулой 6 X 4: гайкой подшипников и контргайкой, между которыми установлены две шайбы, предотвращающие самоотворачивание гаек.
Централизованная пневмосистема автомобилей КамАЗ-4310 позволяет регулировать давление в шинах из кабины в пределах 80...320 кПа в зависимости от дорожных условий. Запасное колесо на этом автомобиле установлено за кабиной в специальном держателе, имеющем механизм опускания и подъема колеса с гидравлическим приводом.
Для снятия запасного колеса надо отсоединить стяжные винты, установить рукоятки на насосе в положение «Опускание запасного колеса» и опустить колесо. Для подъема запасного колеса следует установить его в откидном кронштейне держателя и, качая рукоятку насоса при положении «Подъем запасного колеса», поднять колесо и закрепить стяжными винтами. Положение рукояток для подъема и опускания запасного колеса показано в табличке на насосе.
На автомобилях КамАЗ-43105 держатель запасного колеса установлен на внутренней стороне переднего борта платформы. Для подъема запасного колеса предусмотрена съемная лебедка.
autoruk.ru
Размер по роликам зубчатого колеса. Расчет в Excel.
Опубликовано 02 Июл 2014Рубрика: Механика | 40 комментариев
Программа расчета в Excel размера по роликам (шарикам) зубчатого колеса, представленная в этой статье является универсальной! С ее помощью можно за очень короткое время произвести расчеты для прямозубого или косозубого колеса с наружными или с внутренними зубьями,...
...выполненного без смещения или со смещением исходного контура.
Информация, представленная ниже, может быть полезной студентам-машиностроителям, инженерам-конструкторам и инженерам-технологам (механикам), зубофрезеровщикам и зубошлифовщикам, соответствующим специалистам отделов технического контроля.
Размер по роликам (шарикам) зубчатого колеса относится к размерам для контроля взаимного положения разноименных профилей зубьев и регламентируется Таблицей 3 ГОСТ 16532-70 для передач зубчатых цилиндрических эвольвентных внешнего зацепления и Таблицей 4 ГОСТ 19274-73 для передач внутреннего зацепления.
В этих таблицах представлены формулы и алгоритмы расчетов для пяти параметров:
1. Расчет постоянной хорды зуба и высоты до постоянной хорды.
2. Расчет длины общей нормали.
3. Расчет толщины по хорде зуба и высоты до хорды.
4. Расчет размера по роликам (шарикам).
5. Расчет нормальной толщины.
Выбор контрольного параметра ГОСТами не регламентируется. То есть на чертеже может быть указан любой «понравившийся» конструктору. На практике очень часто – это второй или четвертый. Причем для менее точных передач широко используется длина общей нормали (программу расчета длины общей нормали можно скачать здесь), а для более точных зубчатых передач чаще вычисляют размеры по роликам (шарикам).
Перед тем, как приступить к расчетам, обращаю ваше внимание, что при помощи роликов измеряют контрольный размер только прямозубых колес! Для контроля косозубых колес необходимо использовать шарики!!! Ролики «неправильно» размещаются во впадине между косыми зубьями!
Ролики можно выбрать по ГОСТ 2475-88.
Размер по роликам зубчатого колеса. Универсальный расчет в Excel.
Приступаем к расчетам, запустив программу MS Excel. Если на вашем компьютере не установлена программа MS Excel, то можно выполнить расчет в программе Calc из свободно распространяемых пакетов Apache OpenOffice или LibreOffice.
Схемы измерений показаны ниже на рисунке. Все замеры выполняются в плоскости торцевого сечения колеса!
Рассмотрим в качестве примера расчет размера по шарикам для косозубого колеса с наружными зубьями.
Исходные данные:
1. Документ, регламентирующий нормальный исходный контур зубьев колеса вписываем
в объединенную ячейку C3D3E3: ГОСТ 13755-82
В примечания к ячейке указаны главные параметры контура
α=20° — угол профиля
ha*=1 – коэффициент высоты головки зуба
c*=0,25 – коэффициент радиального зазора
2. Угол нормального исходного контура α в градусах, участвующий в дальнейших расчетах, записываем
в ячейку D4: 20
3. Параметр T, определяющий тип зубьев (наружные или внутренние), вписываем
в ячейку D5: 1
Т=1 — для наружных зубьев
Т=-1 — для внутренних зубьев
4. Модуль зацепления m в миллиметрах пишем
в ячейку D6: 2,00
5. Число зубьев z, контролируемого колеса записываем
в ячейку D7: 27
6. Угол наклона зубьев колеса β в градусах пишем
в ячейку D8: 16,1161
7. Коэффициент смещения исходного контура колеса x вводим
в ячейку D9: 0,400
8. Расчетный диаметр измерительных роликов (шариков) Dр в миллиметрах вычисляем
в ячейке D10: =1,7*D6=3,400
Dр=1,7*m
9. Выбираем ближайший к расчетному диаметр шариков D в миллиметрах из имеющихся в наличии и вписываем
в ячейку D11: 3,690
Выбранные шарики, конечно, не должны лежать на дне впадин и должны выступать за наружный диаметр зубьев!
Шарики (ролики) всегда должны соприкасаться с эвольвентой зубьев!
Результаты расчетов:
10. Угол профиля αtв градусах вычисляем
в ячейке D13: =ATAN (TAN (D4/180*ПИ())/COS (D8/180*ПИ()))/ПИ()*180 =20,7496
αt=arctg (tg (α)/cos (β))
11. Размер по роликам (шарикам) M в миллиметрах рассчитываем
в ячейке D14: =ЕСЛИ(ЧЁТН(D7) -D7=0;J3+D5*D11;ЕСЛИ(D8=0;J3*COS ( ПИ()/(2*D7))+D5*D11;J3*((M14^2+(2*K3*COS ((ПИ()/D7+M14)/2))^2) ^0,5)/(2*K3)+D5*D11))=63,000
M=dD+T*D – для всех колес с четным числом зубьев
M=dD*cos(π/(2*z))+T*D – для прямозубых колес с нечетным числом зубьев
M=dD*((λ2+(2*tg(βD)*cos((π/z+λ)/2))2)0,5/(2*tg(βD))+T*D – для косозубых колес с нечетным числом зубьев
Задача решена! Размер по роликам зубчатого колеса найден! (Точнее – в нашем примере – это размер по шарикам.)
Я умышленно в основную таблицу расчетов не стал включать громоздкие и весьма непростые вспомогательные вычисления, без которых выполнить этот расчет невозможно. Сейчас мы с ними ознакомимся.
Вспомогательные расчеты:
1. Инволюту угла профиля в точке на концентрической окружности зубчатого колеса, проходящей через центры роликов (шариков) inv(αD) вычисляем
в ячейке G3: =TAN (D13/180*ПИ()) -D13/180*ПИ()+D5*(2*D5*D9*TAN (D4/180*ПИ()) -ПИ()/2+D11/(D6*COS (D4/180*ПИ())))/D7=0,042035
inv(αD)=tg(αt) -αt+T*(2*T*x*tg(α) — π/2+D/(m*cos(α)))/z
2. Угол профиля в точке на концентрической окружности зубчатого колеса, проходящей через центры роликов (шариков) αD в радианах считываем
в ячейке I14: =I13- (TAN (I13) -I13-$G$3)/(1/(COS (I13)^2) -1) =0,485187891
Для определения αD решаем уравнение inv(αD)=tg(αD) — αD
Решается это трансцендентное уравнение итерационным методом касательных Ньютона. Подробнее о том, как это делается можно прочитать в статье «Трансцендентные уравнения? «Подбор параметра» в Excel!».
αD(0)=π/4=3.14/4=0,785398163
n=0…11
αD(n+1)= αD(n)— (tg(αD(n)) -αD(n)— inv(αD))/(1/((cos(αD(n)))2-1))
3. Диаметр концентрической окружности зубчатого колеса, проходящей через центры роликов (шариков) dD в миллиметрах рассчитываем
в ячейке J3: =D6*D7*COS (D13/180*ПИ())/(COS (I14)*COS (D8/180* ПИ()))=59,421
dD=m*z*cos (αt/(cos (αD)*cos (β))
4. Параметр tg(βD)определяем
в ячейке K3: =COS (D13/180*ПИ())*TAN (D8/180*ПИ()/COS (I14)) =0,307797
tg(βD)= cos (αt)*tg (β)/cos (αD)
5. Значение параметра λ считываем
в ячейке M14: =M13- (SIN (ПИ()/$D$7+M13)*($K$3^2) -M13)/(COS (ПИ()/ $D$7+M13)*($K$3^2) -1)=0,012140062
Для определения λ решаем уравнение sin(π/z+λ)*(tg(βD))2-λ=0
Решается это трансцендентное уравнение итерационным методом касательных Ньютона – так же, как и уравнение в п.2 этого раздела статьи. (Хотя следует заметить, что есть еще целый ряд методов численного решения подобных уравнений.)
λ(0)=π=3.141592654
n=0…11
λ(n+1)= λ(n)— (sin(π/z+λ(n))*(tg(βD))2-λ(n))/(cos(π/z+λ(n))*(tg(βD))2-1)
Заключение.
При контроле изготовленных зубчатых колес сравниваются измеренные микрометром и рассчитанные значения размеров по роликам (шарикам).
Допуски на размеры по роликам (шарикам) назначаются по ГОСТ 1643-81 в зависимости от требований к передаче.
Теме зубчатых колес на блоге посвящено еще несколько важных и, думаю, полезных статей в рубрике «Механика». Быстро найти их вы сможете в перечне на странице «Все статьи блога».
Для получения информации о выходе новых статей и для скачивания рабочих файлов программ прошу вас подписаться на анонсы в окне, расположенном в конце статьи или в окне вверху страницы.
Уважаемые читатели, вопросы, отзывы, и замечания оставляйте в комментариях внизу страницы.
Прошу УВАЖАЮЩИХ труд автора скачать файл ПОСЛЕ ПОДПИСКИ на анонсы статей!
Ссылка на скачивание файла: raschet-razmera-po-rolikam (xls 37.0KB).
Другие статьи автора блога
На главную
Статьи с близкой тематикой
Отзывы
al-vo.ru
Колесо: конструкция и параметры
Колесо: конструкция и параметрыВылетВылет колеса - это расстояние между монтажной поверхностью, которой диск прилегает к ступице колеса, и центральной плоскостью диска. Положительный вылет означает, что плоскость прилегания колеса к ступице находится перед центральной плоскостью диска. Визуально это означает, что колесо с большим отрицательным вылетом будет выступать за крыло автомобиля, с положительным - будет утоплено внутрь. Но есть еще и другие особенности. При значительном уменьшении вылета возрастает длина плеча обката. Это приводит к нестабильности управления автомобилем: на неровностях дороги возникают силы, стремящиеся развернуть колеса наружу. Чем больше плечо приложения этой силы, тем сильнее она передается через элементы управления и руль стремиться вырваться из рук, и тем сложнее управлять автомобилем. Другими словами - чем шире колесная база автомобиля по сравнению со штатной, тем меньше стабильность управления.Кроме того, существенно возрастает нагрузка на подшипники и подвеску. Ее можно оценить так: при уменьшении вылета на 50 мм нагрузка на подвеску возрастает в 1,5 раза.
СверловкаКак правило, литые диски имеют один набор посадочных отверстий. Однако бывает и двойная сверловка: это двойной набор отверстий в одном диске, который делает его более универсальным.Чаще всего сверловка обозначается так: 5/100 или 5х100. “5” обозначает количество крепежных отверстий, “100” означает диаметр окружности, проходящей через центры крепежный отверстий. Для четного количества отверстий этот параметр измерить не сложно, достаточно лишь замерить расстояние между центрами противоположных отверстий. Для нечетного количества отверстий все несколько сложнее, поэтому проще посмотреть выбитые на обороте колеса значения этих параметров.
Центральное отверстиеСамое важное - центральное отверстие должно быть не меньше, чем диаметр ступицы автомобиля. В широкой продаже часто встречаются колесные диски с центральным отверстием большого диаметра, чтобы сделать диск универсальным и устанавливаемым на широкий круг автомобилей. В этом случае рекомендуется использовать переходные кольца, которые позволяют уменьшить центральное отверстие до необходимого значения. Как правило они сделаны из металла или твердого пластика. Это не должно вводить в заблуждение: вся нагрузка ложится на болты, которыми колесо крепится к автомобилю. Переходные кольца служат только для облегчения центровки колес при установки на машину. Для колес с креплением на 6 отверстий центровочные кольца не обязательны.
Ширина колесного дискаОбычно ширина колесного диска измеряется в дюймах между внутренними поверхностями бортиков. Чаще всего ширина диска привязана к его диаметру: чем больше диаметр диска, тем больше может быть его ширина. От ширины колесного диска зависит и диапазон допустимых размеров ширины шины. Этот диапазон расширяется с увеличением профиля покрышки. Чем выше профиль, тем больше разница между минимальным и максимальным значением ширины колесного диска. Воспользуйтесь шинным калькулятором на нашем сайте - он поможет правильно выбрать оптимальные параметры колеса.
Диаметр колесного дискаДиаметр колесного диска выражается в дюймах. Очень часто диаметр диска ошибочно называют радиусом. Это пошло с тех времен, когда конструкция корда шин была разного типа: диагональная и радиальная. Впоследствии радиальные шины полностью вытеснили диагональные, но обозначение латинской буквой R перед значением диаметра шины осталось. Это и привело к ошибочному называнию диаметра шины или диска радиусом. Конечно же, диаметр диска должен совпадать с диаметром монтируемой на него шины. Нельзя устанавливать шины диаметром 16,5 дюймов на 16”-ые диски.
Диаметр колесаПри увеличении или уменьшении диаметра диска необходимо помнить, что новые шины могут иметь другой внешний диаметр. Поэтому важно подобрать такой размер шин, чтобы внешний диаметр колеса не изменился. Для точного расчета вы можете воспользоваться шинным калькулятором на нашем сайте, но так же существует примерное правило для вычисления нового размера шин для легковых авто.
Правило следующее:
Если вы хотите увеличить диаметр колесного диска на один дюйм, тогда:1. увеличьте штатный размер шины на 20 мм,2. уменьшите высоту шины на 10 единиц,3. увеличьте диаметр шины и диска на 1 дюйм.
Например, у вас стоят диски 15” и шина 195/65 R15.Новые параметры колеса будут следующие: 16” диск и 205/55 R16 шина.В этом случае отклонение в размере колеса не превысит нескольких мм.
Крепление колесаТолщина стенок и других элементов литого диска больше, чем у штампованного. Поэтому болты для крепление литых колес должны быть длиннее, чем для штампованных. Для надежного крепления колеса болт должен затягиваться как минимум на 8 оборотов резьбы. Силу затягивания болтов следует сверить с инструкцией на автомобиль и после установки колес через 150 км пробега необходимо проверить затяжение болтов и убедиться, что оно не ослабло.
Следует внимательно проверять соответствие формы болтов и посадочных отверстий. Как правило, болты бывают сферическими и коническими. Крепление колеса с коническими отверстиями на сферические болты может привести к его деформации, вибрациям при движении и повреждением резьбы.
Перестановка шинПоскольку каждая шина автомобиля как правило нагружена несколько разным весом, а стиль вождения каждого водителя имеет свои характерные особенности, то каждая шина изнашивается по-разному. Поэтому важно менять местами шины каждые 8-12 тысяч километров. Способ перестановки шин зависит от типа автомобиля. На схемах показаны оптимальные способы перестановки шин.
Конечно же, если ваш автомобиль имеет разные размерности передних и задних колес, то в этом случае перестановка возможна путем замены левого колеса на правое на одной оси и наоборот.
Другие публикации
Грязевая резина на УАЗ "Буханку"В этой статье мы постараемся подробно рассказать о том, какие шины лучше всего подойдут на УАЗик, который в народе называют "Буханка"
samohodoff.ru
Конструирование зубчатых колес
При конструировании зубчатого колеса учитывают материал, из которого оно будет изготовлено, требуемый диаметр и способ получения заготовки.
Стальные зубчатые колеса
Зубчатые колеса диаметром до 150 мм в единичном и мелкосерийном производстве обычно изготовляют из круглого проката; в средне-, крупносерийном и массовом производстве предпочтительнее применять кованые или штампованные заготовки, имеющие более высокие механические характеристики.
Шестерни изготовляют за одно целое с валом (вал-шестерня) (рис. 1, а, б) или делают съемными, если расстояние χ от впадины зуба до шпоночного паза (рис. 2) больше 2,5 mn для цилиндрических шестерен и 1,8 me для конических. В случае цельной конструкции увеличивается жесткость вала и уменьшается общая стоимость вала и шестерни. Разъемная конструкция позволяет выполнить шестерню и вал из разных материалов, а при поломке одной детали вторую оставить без замены. На рис. 1, а показана конструкция вала-шестерни, когда диаметр впадин зубьев df1 превышает диаметр вала dб.п. (диаметр буртика подшипника), что обеспечивает свободный выход инструмента при нарезании зубьев. При df1 < dб.п. (рис. 1, б) выход фрезы lвых определяют прочерчиванием по ее наружному диаметру Dф, который принимают по табл. 1 в зависимости от mn и степени точности передачи.
Цилиндрические зубчатые колеса диаметром до 400... 500 мм (в отдельных случаях до 600 мм) можно выполнять коваными, штампованными, литыми или сварными.
Конструктивные элементы зубчатых колес показаны на рис. 3.
Типовые конструкции зубчатых колес и основные соотношения их элементов даны на рис. 4—8. Кованые заготовки для зубчатых колес применяют при наружном диаметре колеса 4,df < 200 мм или при нешироких колесах (ψba < 0,2) диаметром da до 400 мм. Операция штамповки отличается высокой производительностью и максимально приближает форму заготовки к форме готового колеса. Для облегчения заполнения металлом и освобождения от заготовки штамп, а следовательно, и заготовка должны иметь радиусы закруглений r ≥ 5 мм и штамповочные уклоны γ ≥ 5° (рис. 4). Внутреннюю поверхность обода, наружную поверхность ступицы и поверхности диска штампованных колес обычно не обрабатывают. Конструкция литого колеса дана на рис. 5.
Таблица 1. Значения диаметра фрезы Dф, мм СтепеньпрочностипередачиНоминальный модуль mn, мм2...2,25 | 2,25...2,75 | 3...3,75 | 4...4,5 | 5...5,5 | 6...7 | |
78...10 | 9070 | 10080 | 11290 | 125100 | 140112 | 160125 |
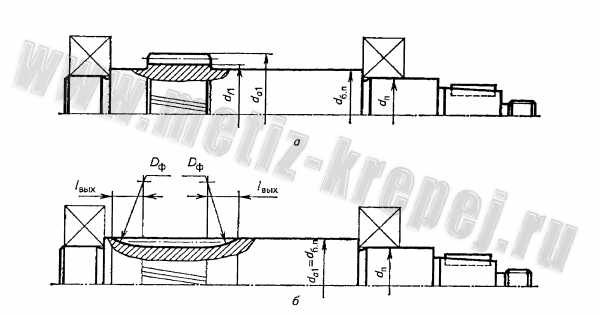
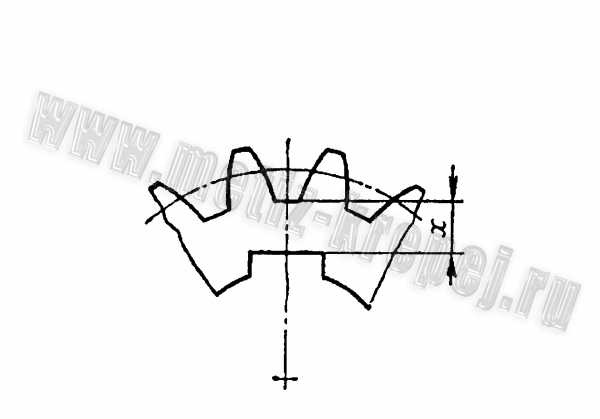
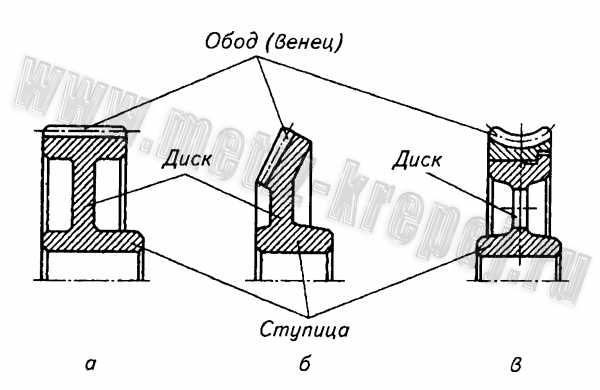
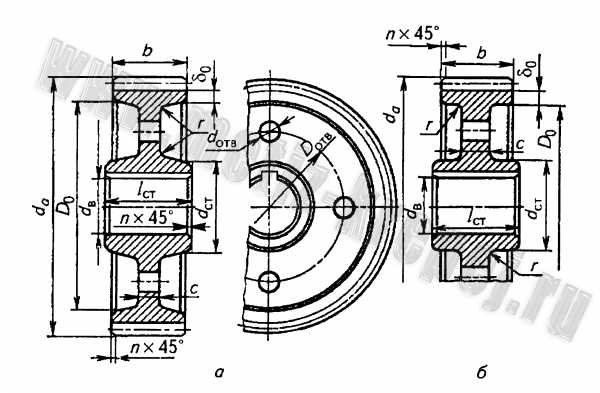
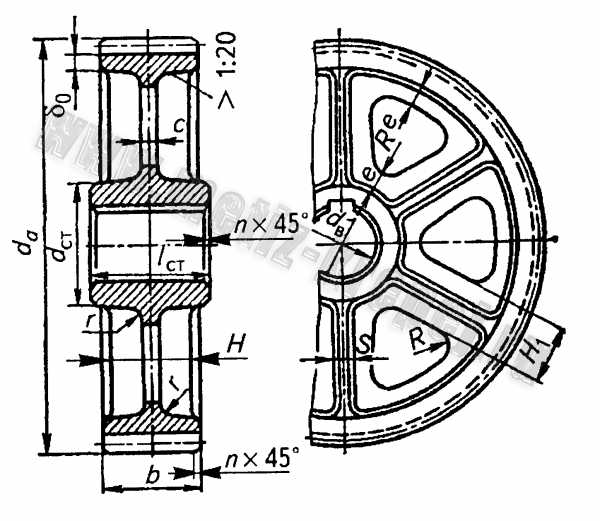
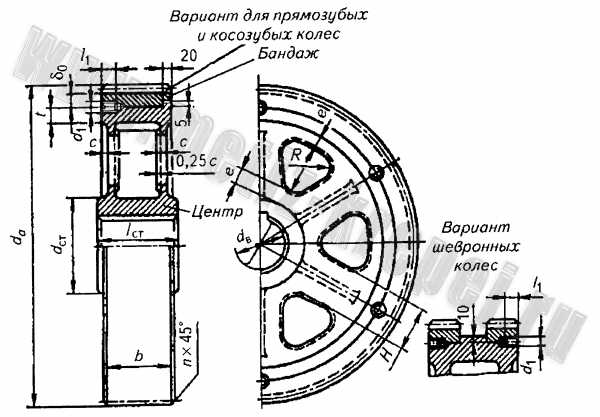
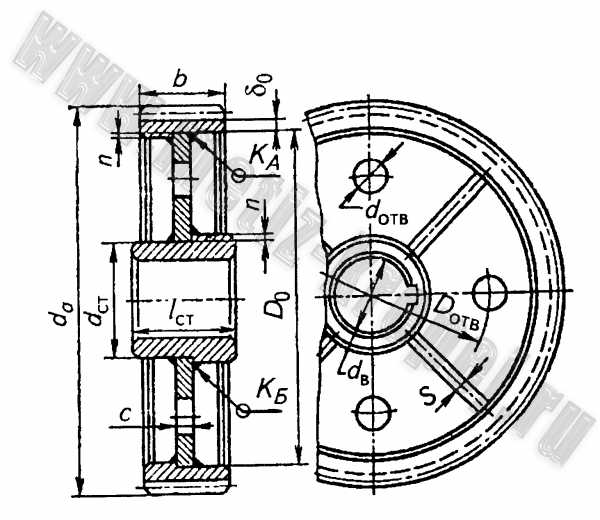
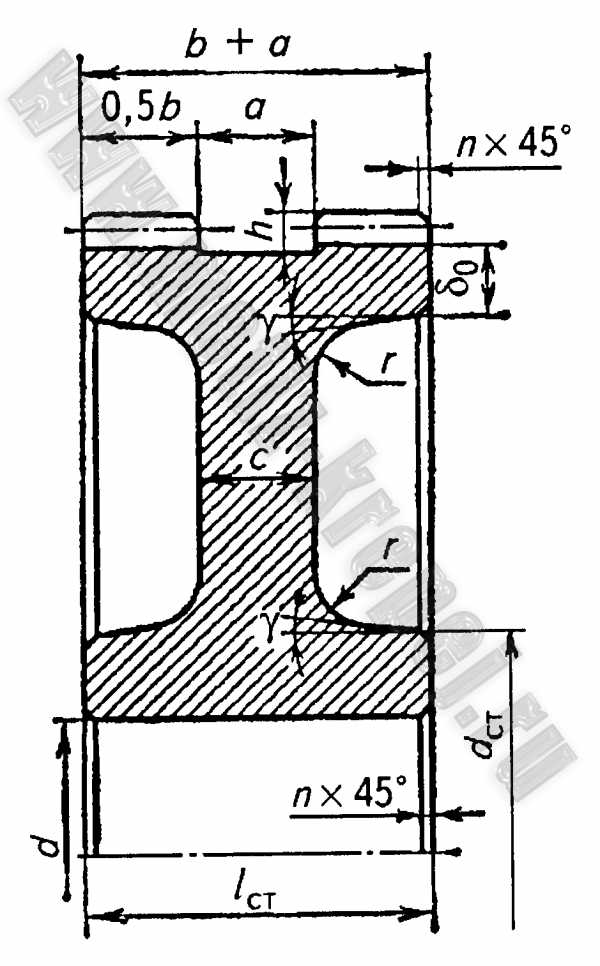
Размеры ступицы выбирают по рекомендациям, приведенным под рисунками. Длину ступицы lст по возможности принимают равной ширине венца колеса b, что обеспечивает наименьшую ширину редуктора. Отношение длины ступицы к диаметру вала должно быть не меньше 0,5. При отношении меньше 0,8 на валу предусматривают буртик, исключающий торцевое биение колеса, к которому будет прижиматься торец ступицы колеса. Если по условиям расчета (см. расчет шпоночного и шлицевого соединений) lст> b, то ступицу желательно сместить по оси колеса до совпадения одного ее торца с торцом венца (см. рис. 3, а), что дает возможность нарезать зубья сразу на двух колесах. Реже (для одноступенчатых редукторов) колеса изготовляют со ступицей, выступающей в обе стороны относительно венца (рис. 3, в), при этом зубья можно нарезать только на одном колесе. При одинаковой длине ступицы и ширине венца можно одновременно нарезать зубья на нескольких колесах.
С целью экономии материала, при больших диаметрах колес, для соединения ступицы с венцом колеса вместо сплошного диска применяют спицы. Зубчатые колеса большого диаметра (при внешнем диаметре da≥ 600 мм) иногда делают бандажированными (рис. 6): венец — стальной кованый (бандаж), а колесный центр — из стального или чугунного литья. Венец сопрягается с колесным центром посадкой с гарантированным натягом. Для большей надежности в плоскости соединения венца с центром ставят винты; соединения проверяют на смятие по материалу колесного центра: при стальном колесном центре [σ] см≥ 0,3σ т, при чугунном [σ] см≥ 0,4σ в.и, где σ т — предел текучести; σ в.и — предел прочности чугуна на изгиб.
При индивидуальном изготовлении колёса иногда делают сварными (рис. 7). При диаметре da≥ 1500 мм для удобства сборки зубчатые колеса делают разъемными — из двух половин.
На торцах зубьев и обода выполняют фаски n = 0,5mn, размер которых округляют до стандартного значения 1; 1,2; 1,6; 2; 2,5; 3; 4; 5.
Острые кромки на торцах ступицы притупляют фасками n x 45, размер которых принимают в зависимости от диаметра вала d:
d, ммn, мм | 20...301 | 30...401,2 | 40...501,6 | 50...802 |
Продолжение | ||||
d, ммn, мм | 80...1202,5 | 120...1503 | 150...2504 | 250...5005 |
Шевронные зубчатые колеса (рис. 8) отличаются от других цилиндрических колес большей шириной. Наиболее часто шевронные колеса изготовляют с канавкой посередине, предназначенной для выхода червячной фрезы, нарезающей зубья. При известных размерах фрезы ширину канавки a определяют прочерчиванием. Приближенно размер а можно определить в зависимости от модуля m:
m, ммa, мм | 1,527 | 232 | 2,537 | 342 | 3,547 | 453 | 560 | 667 | 775 | 885 | 10100 |
Остальные конструктивные элементы шевронных колес принимают по соотношениям, указанным под рис. 8.
Конические зубчатые колеса изготовляют коваными, штампованными, литыми или из круглого проката (рис. 9—11).
Конические колеса с внешним диаметром вершин зубьев dae< 120 мм конструируют, как показано на рис. 9. В том случае, когда угол делительного конуса σ < 30 °, колесо выполняют по рис. 9, а, при σ < 45 ° — по рис. 9, б. Если 30° ≤ σ ≤ 45° , можно использовать обе формы. Штампованные колеса (рис. 10, а) применяют в серийном производстве. При внешнем диаметре вершин dae≥ 300 мм используют также литые конические колеса с ребрами жесткости.
Ступицу в зубчатых конических колесах необходимо располагать так, чтобы при закреплении колеса на оправке для нарезания зубьев обеспечивался зазор а> 0,5 mte для свободного выхода инструмента, где т,е внешний окружной модуль (рис. 11).
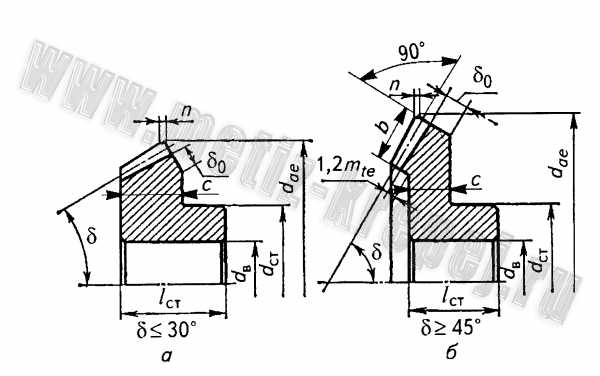
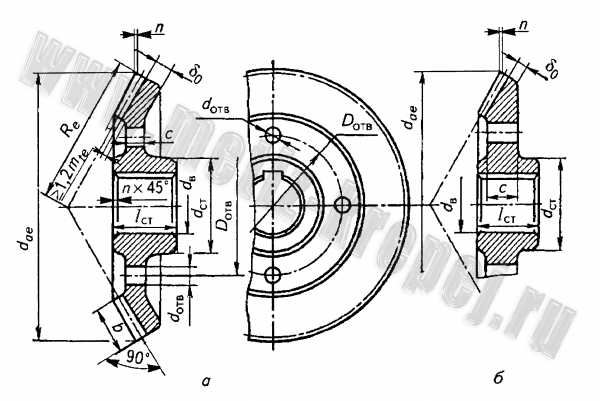
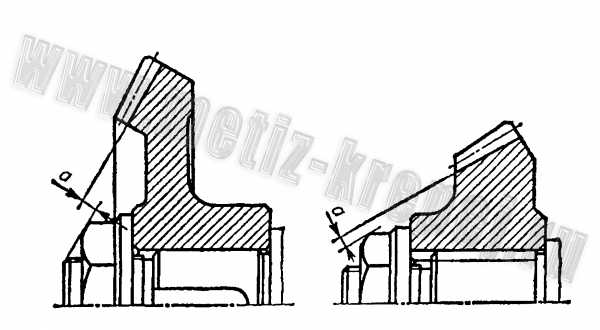
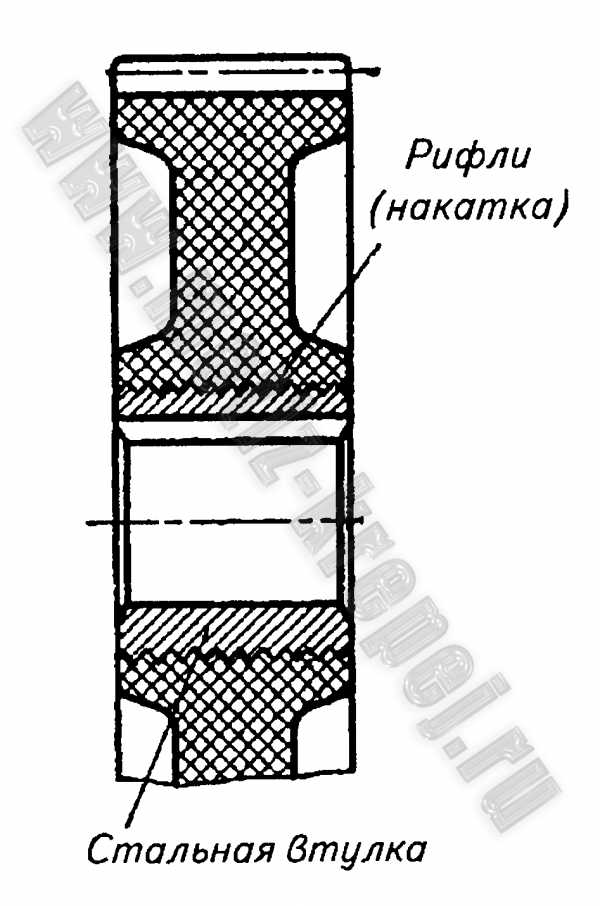
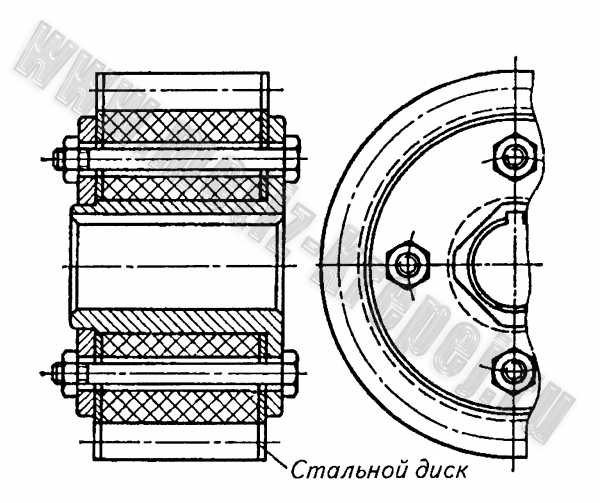
В дисках цилиндрических и конических зубчатых колес предусматривают отверстия диаметром dотв, используемые для закрепления при обработке на станках и при транспортировке. При больших размерах отверстий они служат для уменьшения массы колес, а в литых колесах также для выхода литейных газов при отливке.
Неметаллические зубчатые колеса.
Неметаллические зубчатые колеса. Зубчатые колеса из пластмасс (текстолит, древопластики, полиамиды и т. п.) работают более бесшумно, чем металлические, что имеет особое значение при больших скоростях. Чтобы понизить коэффициент трения между зубьями, одно зубчатое колесо делают из пластмассы, а второе выполняют металлическим. Пластмассы имеют сравнительно небольшие сопротивления срезу и смятию, поэтому в большинстве случаев для передачи момента применяют стальную втулку-ступицу, прочно соединяемую с телом колеса. В небольшие колеса ступицу устанавливают при формовании. Для лучшего сцепления наружную поверхность ступицы делают рифленой (накатанной) (рис. 12). Чтобы предотвратить выкрашивание и откалывание отдельных слоев пластмассы, края зубьев защищают стальными дисками (рис. 13). Толщину диска рекомендуется принимать равной половине модуля, но не более 8 мм и не менее 2 мм. Материал дисков —сталь Ст.2, Ст.З.
Зубчатые колеса больших размеров обычно делают сборными из отдельных секций.
Ширину зубчатого колеса из пластмасс принимают равной ширине зацепляющегося с ним металлического колеса или несколько меньше во избежание местного износа и выработки зубьев
metiz-bearing.ru
- Тест драйв кордиант сноу кросс
- Диски для вольво s60
- Кордиант официальный сайт производитель
- Золотник или ниппель
- Тесты летних шин 2018 для внедорожников
- Кордиант официальный сайт производитель
- Золотник или ниппель
- Avon шины
- Какое давление в шинах должно быть зимой
- Повторная ошиповка зимних шин своими руками
- Выставка iaa 2018